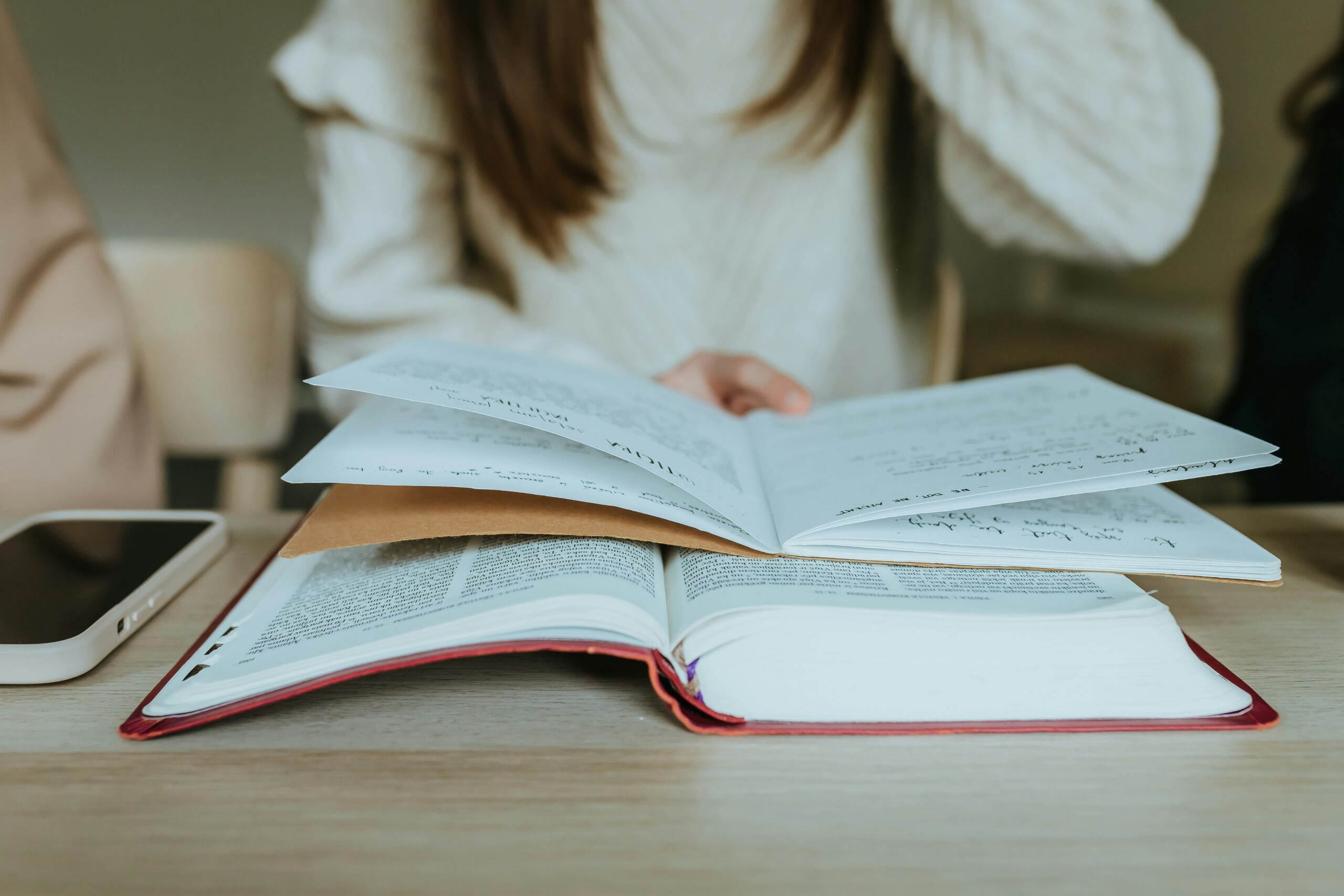
In today’s competitive business landscape, operational excellence is more than just a buzzword; it is a fundamental strategy for achieving sustained success. Companies prioritizing operational excellence often outperform their competitors by delivering higher-quality products and services, improving customer satisfaction, and driving greater profitability. But what does operational excellence mean, and how can organizations achieve it? This guide provides a thorough overview of operational excellence, breaking down its importance and the steps to implement it.
The Core Principles of Operational Excellence
Operational excellence refers to the continuous effort to improve business processes’ efficiency, effectiveness, and quality. It ensures that every aspect of an organization’s operations works seamlessly and contributes to achieving business goals. Several key principles underpin operational excellence:
- Customer Focus: The ultimate goal is to meet or exceed customer expectations. Companies must understand their customers’ needs and preferences and deliver products and services that meet those requirements.
- Continuous Improvement: Operational excellence is a journey, not a destination. It involves regularly assessing and improving processes to eliminate waste, reduce costs, and enhance performance.
- Employee Engagement: Employees at all levels should be involved in improving operations. Their insights and suggestions are invaluable in identifying inefficiencies and finding creative solutions.
- Leadership Commitment: Leaders must drive change and create a culture of excellence. Their commitment to operational excellence sets the tone for the entire organization.
- Data-Driven Decisions: Decisions should be based on accurate data, not assumptions. By utilizing performance metrics, businesses can track progress and make informed decisions.
Organizations can create a strong foundation for operational excellence and drive long-term success by focusing on these principles.
Building a Culture of Operational Excellence
Creating a culture that supports operational excellence requires more than just adopting a few new practices or processes. It involves embedding a mindset of continuous improvement into the organization’s DNA. This culture shift begins with leadership but must extend throughout all company levels.
Leaders play a critical role in fostering this culture by setting clear expectations, communicating the importance of operational excellence, and supporting employees to improve. They should provide the necessary resources and training to ensure employees have the tools and knowledge to succeed. Encouraging open communication and collaboration across departments is also essential in breaking down silos and fostering a culture of teamwork and shared responsibility.
At the employee level, a culture of operational excellence means empowering individuals to take ownership of their work and constantly seek ways to improve their performance. This might include encouraging employees to identify bottlenecks or inefficiencies in processes, suggest improvements, and participate in training sessions to enhance skills and knowledge.
When every organization member is aligned with operational excellence, the company can achieve higher productivity, efficiency, and innovation.
Implementing Lean and Six Sigma Methodologies
Two popular methodologies for achieving operational excellence are Lean and Six Sigma. These approaches focus on eliminating waste, reducing variation, and improving overall efficiency in business processes.
- Lean: Lean methodology aims to maximize value by minimizing waste. Waste can come in many forms, such as overproduction, waiting times, unnecessary motion, and defects. By identifying and eliminating waste, companies can streamline operations, reduce costs, and improve quality. Lean also encourages a focus on customer value, ensuring that resources are allocated efficiently to deliver the most value to customers.
- Six Sigma: Six Sigma is a data-driven methodology that reduces defects and process variation. The goal is to achieve near-perfect quality by minimizing errors and inconsistencies. Six Sigma uses statistical tools and techniques to analyze data and identify the root causes of problems. By addressing these root causes, companies can make informed decisions and drive significant improvements in their operations.
Many organizations implement both Lean and Six Sigma together, often called Lean Six Sigma. This combination leverages the strengths of both methodologies to drive continuous improvement and achieve operational excellence.
The Role of Technology in Operational Excellence
Technology plays a vital role in achieving operational excellence in today’s digital world. Advances in automation, artificial intelligence (AI), and data analytics have provided businesses with powerful tools to streamline operations and improve decision-making.
- Automation: Automation technologies, such as robotic process automation (RPA), can help eliminate manual, repetitive tasks. This reduces the risk of human error and frees up employees to focus on more value-added activities. By automating routine processes, businesses can improve efficiency and reduce costs.
- Data Analytics: Data analytics allows companies to collect and analyze vast amounts of information in real-time. Businesses can identify trends, monitor performance, and make more informed decisions by leveraging data. Predictive analytics can also help organizations anticipate issues before they arise, enabling proactive problem-solving.
- Artificial Intelligence (AI): AI-powered systems can optimize processes by learning from data and making decisions without human intervention. For example, AI can help improve supply chain management by predicting demand, optimizing inventory levels, and identifying potential disruptions.
When used effectively, technology can significantly accelerate the journey toward operational excellence. However, organizations must ensure that technology is integrated into existing processes and that employees are trained to use these tools effectively.
Measuring Success in Operational Excellence
To determine whether an organization is achieving operational excellence, tracking progress through measurable performance indicators is essential. These key performance indicators (KPIs) provide valuable insights into how well the organization is performing and where improvements are needed.
Common KPIs for operational excellence include:
- Quality Metrics: These measure the defect rate, customer complaints, and the overall quality of products or services.
- Efficiency Metrics: These track how healthy resources are used, including cycle time, throughput, and productivity.
- Cost Metrics: These focus on cost reduction, including cost per unit, cost savings, and return on investment.
- Customer Satisfaction Metrics: These measure how well the organization meets customer expectations, including Net Promoter Scores (NPS) and customer feedback surveys.
Regularly monitoring these KPIs allows organizations to identify areas where performance is lagging and take corrective actions. Additionally, measuring progress helps to keep the organization focused on its goals and reinforces the commitment to continuous improvement.
The Path to Lasting Operational Excellence
Achieving operational excellence is not a one-time initiative but an ongoing commitment to improving processes, empowering employees, and meeting customer needs. Organizations can build a culture that supports operational excellence by focusing on key principles such as customer focus, continuous improvement, employee engagement, and data-driven decisions.
Lean and Six Sigma methodologies offer proven frameworks for driving improvement, while technology can accelerate the process by automating tasks and providing valuable insights. By tracking performance through KPIs and continuously making data-driven decisions, companies can ensure they are on the right path to operational excellence.
Organizations that successfully achieve operational excellence will improve their bottom line and build a reputation for delivering high-quality products and services, fostering customer loyalty, and staying ahead of the competition. Ultimately, operational excellence is about creating a sustainable competitive advantage through the efficient and effective use of resources, innovation, and a commitment to excellence at every level of the organization.