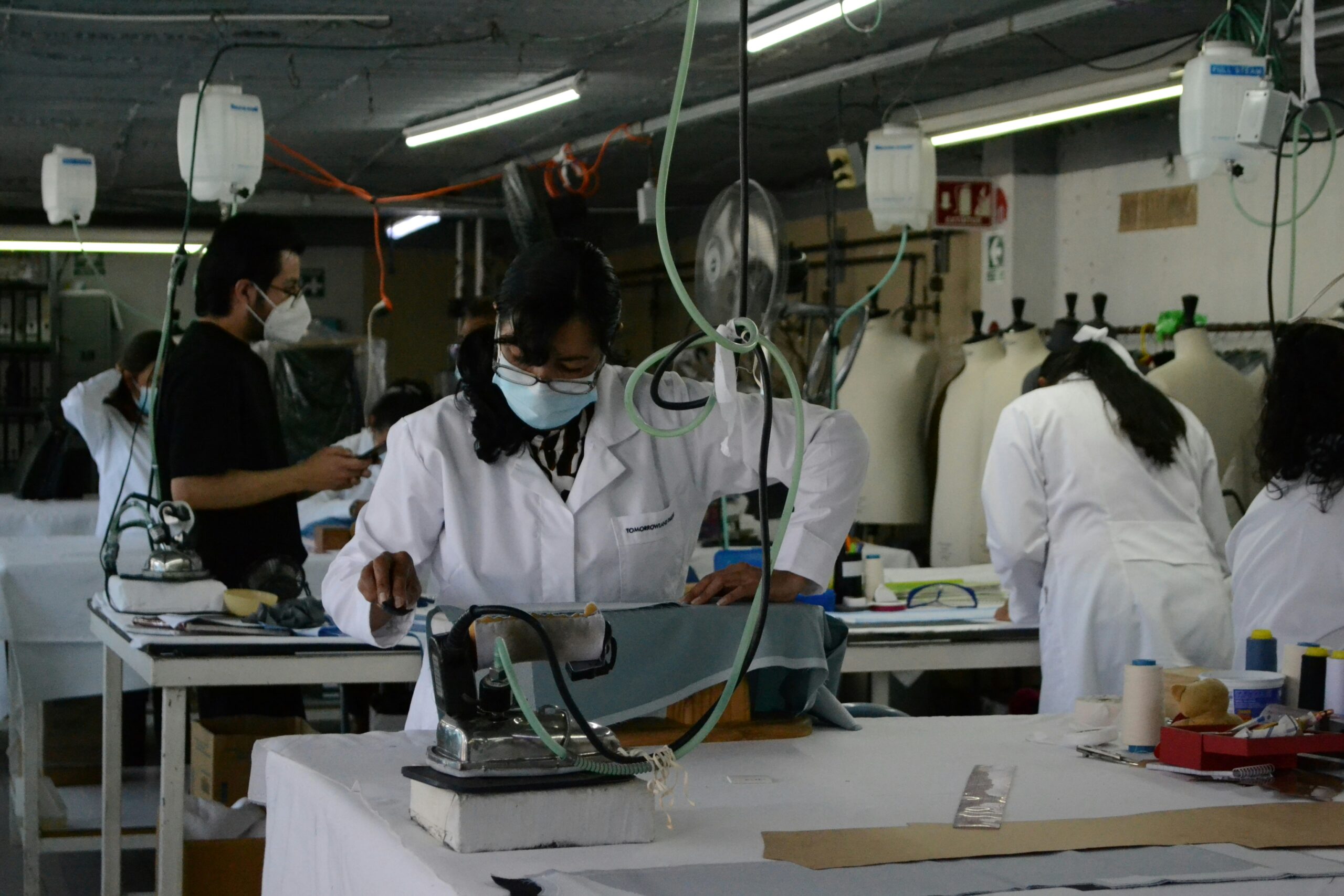
Manufacturing process design is a critical aspect of industrial engineering that directly impacts product quality, cost, and production efficiency. It involves planning, designing, and organizing the various steps of a production system to ensure that products are made as effectively and efficiently as possible. In today’s fast-paced manufacturing environment, businesses must focus on continuous improvement, innovation, and efficiency. To remain competitive, manufacturers must adopt modern technologies, streamline their workflows, and eliminate inefficiencies in their processes.
Understanding Manufacturing Process Design
Manufacturing process design refers to the strategic planning of all activities involved in creating a product, from selecting raw materials to final assembly and packaging. It encompasses multiple stages, including process planning, system integration, and operations management. The goal is to optimize the entire production cycle, ensuring products are manufactured efficiently, meet quality standards, and are produced at competitive costs.
To initiate the process, manufacturers evaluate the product’s requirements, including materials, design specifications, and the desired output. The next step is to determine the most suitable production method, which may involve processes such as assembly lines, batch production, or continuous flow. By selecting the proper process, manufacturers can reduce waste, increase throughput, and improve overall efficiency.
Key Principles of Effective Manufacturing Process Design
Several key principles guide the design of an effective manufacturing process. First and foremost, companies must prioritize flexibility and scalability. As market demands change, manufacturers need the ability to adapt quickly. This may involve incorporating modular components or designing systems that can easily accommodate changes in product volumes or specifications.
Moreover, waste reduction is essential. Waste can take many forms, including excess raw materials, time, energy, or labor. A well-designed manufacturing process ensures that resources are used efficiently, thereby reducing costs. The principles of Lean manufacturing, such as value stream mapping and continuous improvement, are often employed to identify and eliminate waste throughout the production process.
Another essential principle is the consideration of quality control throughout the process. Manufacturers should implement stringent quality checks at various stages to ensure that products meet customer expectations and industry standards. By focusing on quality at every stage, manufacturers can minimize defects, prevent costly rework, and enhance customer satisfaction.
Choosing the Right Technology for Process Design
In the modern manufacturing landscape, technology plays a pivotal role in process design. Automation and digitalization have revolutionized the design and management of manufacturing systems. Using computer-aided design (CAD) and computer-aided manufacturing (CAM) software, manufacturers can simulate, test, and refine processes before implementing them on the shop floor.
Robotics is another technology that enhances process efficiency. Automated robots can perform repetitive tasks with speed and precision, reducing human error and improving consistency. Additionally, the integration of Internet of Things (IoT) sensors into production systems allows manufacturers to collect real-time data, monitor system performance, and make data-driven decisions.
Advanced technologies, such as artificial intelligence (AI) and machine learning, are also being utilized to improve process design. AI algorithms can optimize production schedules, predict maintenance needs, and analyze patterns in production data to identify opportunities for improvement. With these technologies, manufacturers can design processes that not only improve efficiency but also allow for predictive insights and long-term optimization.
The Role of Simulation in Process Design
Simulation is a powerful tool in the design of the manufacturing process. It enables manufacturers to model various scenarios and test different strategies before implementing them in a real-world setting. By utilizing simulation software, manufacturers can pinpoint potential bottlenecks, optimize resource allocation, and make informed decisions regarding production methods.
For instance, discrete event simulation (DES) models the flow of materials and products through a production system, helping manufacturers understand the impact of different process configurations. Similarly, computational fluid dynamics (CFD) simulations can help optimize processes that involve fluid flow, such as in chemical or food manufacturing.
Simulation also allows for the optimization of assembly line layouts. By testing different layouts in a virtual environment, manufacturers can determine which configuration leads to the shortest cycle times and maximum throughput. This reduces trial and error in real-world implementations, saving both time and resources.
Lean Manufacturing and Continuous Improvement
Lean manufacturing principles are integral to modern process design. The core idea behind Lean is to maximize customer value while minimizing waste. By focusing on value-added activities and eliminating non-value-added activities, manufacturers can create more efficient production processes.
A key tool in Lean manufacturing is the “Kaizen” approach, which emphasizes continuous improvement. By consistently reviewing processes and making minor, incremental improvements, manufacturers can achieve long-term gains in efficiency and cost reduction. This culture of constant improvement encourages employees at all levels to identify inefficiencies and suggest solutions.
Implementing Lean principles requires a commitment to long-term change, but the benefits are clear. By reducing waste, improving flow, and minimizing downtime, manufacturers can enhance overall productivity. Furthermore, Lean principles help to foster a culture of collaboration and innovation, as employees work together to solve problems and improve processes.
Challenges in Manufacturing Process Design
While manufacturing process design offers many benefits, it is not without challenges. One of the biggest obstacles is managing the complexity of the design process. As products become more advanced and customer demands grow, manufacturers must juggle multiple variables, including material choices, production methods, equipment, and workforce capabilities.
Additionally, manufacturers must navigate the risks associated with implementing new technologies. While automation and digitalization offer significant advantages, they require substantial upfront investment and training. Furthermore, transitioning to automated systems can disrupt existing workflows and lead to resistance from employees who are accustomed to traditional methods.
Another challenge is maintaining a balance between efficiency and flexibility. While it is essential to streamline processes, manufacturers must also ensure that their systems can accommodate changes in product designs or production schedules. This requires a careful approach to process design, ensuring that systems are both efficient and adaptable.
Conclusion: Striving for Excellence in Manufacturing Process Design
Manufacturing process design is an ongoing journey of optimization, innovation, and continuous improvement. By focusing on efficiency, quality control, and the adoption of modern technologies, manufacturers can create systems that meet both current and future demands. The application of lean principles, simulation tools, and cutting-edge technologies can significantly enhance process design, resulting in improved productivity, reduced costs, and enhanced customer satisfaction.
To succeed in the competitive manufacturing environment, businesses must remain agile and constantly evaluate and improve their processes. By staying focused on streamlining workflows, reducing waste, and incorporating new technologies, manufacturers can ensure that their process designs remain at the forefront of industry standards. Ultimately, the goal is to create a manufacturing process that not only maximizes efficiency but also contributes to sustainable growth and long-term success.